Hot filling is a unique filling method. It expands opportunities for product quality and revenue generation without affecting packaging performance and consumer experience. This innovative filling method is aimed at hot filling (juice, nectar, soft drinks, isotonic drinks, tea) filled to 1.2 liter PET bottles at a temperature of 85-88°C.The whole process adopts computer control, and the production is simple, hygienic and efficient.
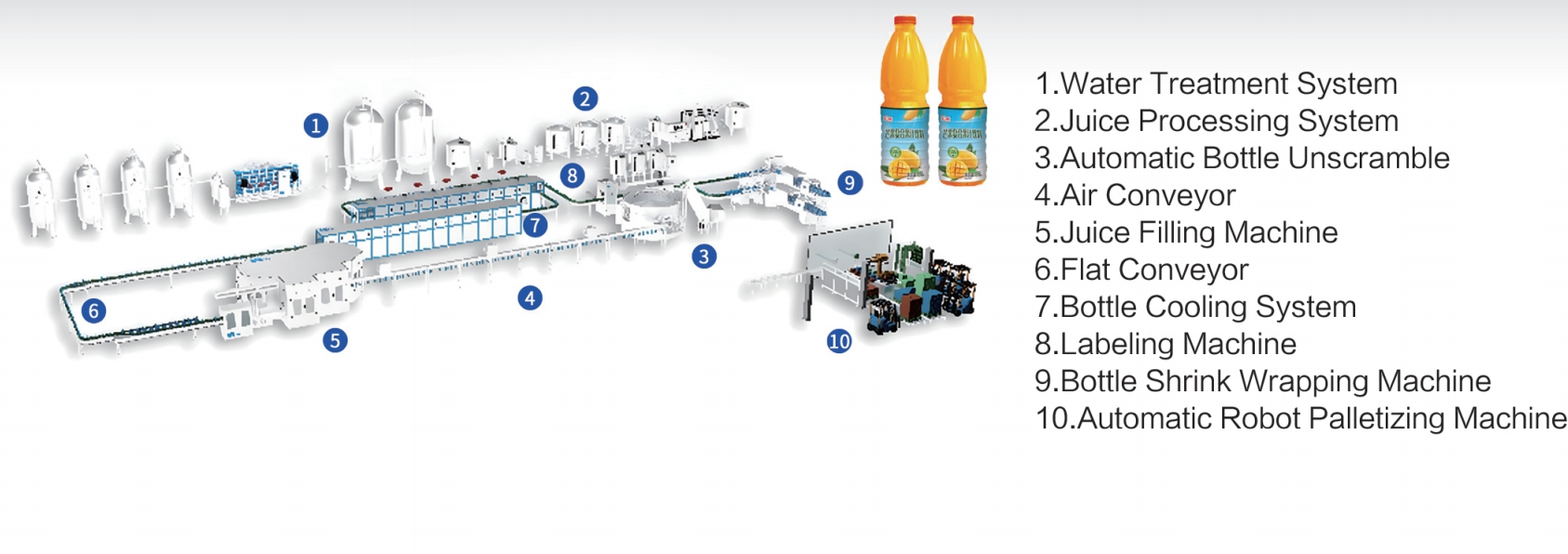
1 - Water Treatment System.
* Raw water tank + Raw water pump
* Silica sand filter + Active carbon filter + Sodium ion exchanger + Precision filter + Security filter
* Reverse Osmosis (one level)
* UV sterilizer
* Finished water tank + Pure water pump
1 / Stainless steel high pressure film shell
2 / All kinds of capacity indicator, pressure indicator, electricity magnetic valve, balance device and pipe valve system
3 / Online type pressure auto self-protection device
4 / Online type electricity indicator (with stable compensation)
5 / System safe protecting and alarm system
6 / System frame
2 - Pre-process System.
1 / High-shear emulsifying tank + Plate heat exchanger
2 / Mixing tank
3 / UHT sterilizer + homogenizer machine + Buffer tank
4 / Hot water system + Hot water tank
5 / CIP cleaning system
3 - Blow Molding Machine.
1 / Blower : Industry-leading blower performance with patented control and self-regulation systems for repeatable and consistently high bottle quality
2 / Production flexibility: Up to 200 different equipment size configurations from one platform
3 / Top quality: Electrical stretching for bottle integrity, full material distribution control and performance
4 / Fast output: Boosted uptime and speed (up to 2,400 bottles/mould/hour)
5 / Efficient consumption: Up to 45 % less electricity and 35 % less compressed air
4 - RCGF Juice Hot Filling Machine.
1 / Enhanced food safety: Stainless steel 304/316L for all components in contact with your beverage
2 / Optimum uptime: 30 % reduction in changeover and maintenance downtime
3 / Sustainable solution: Reduced filler enclosure and servomotors reduce resource consumption
4 / Hygiene improvement through volume control and contactless filling
5 / Automatic dummy bottles: Safer, easier cleaning procedures
6 / Automatic bottle changeover improves uptime
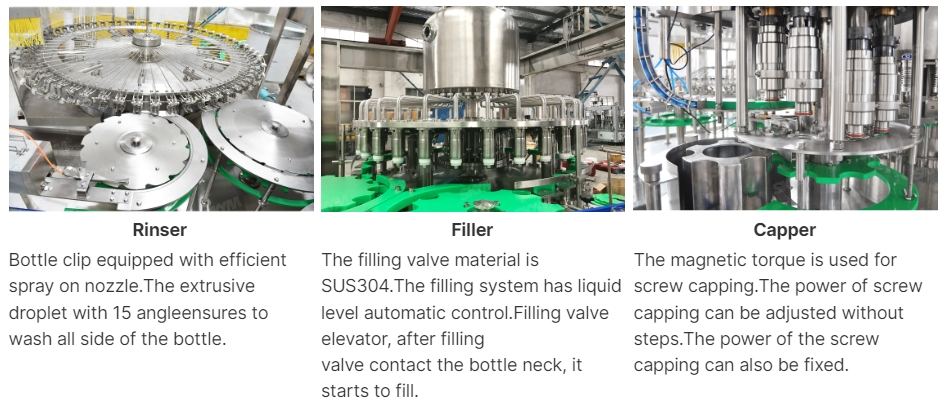
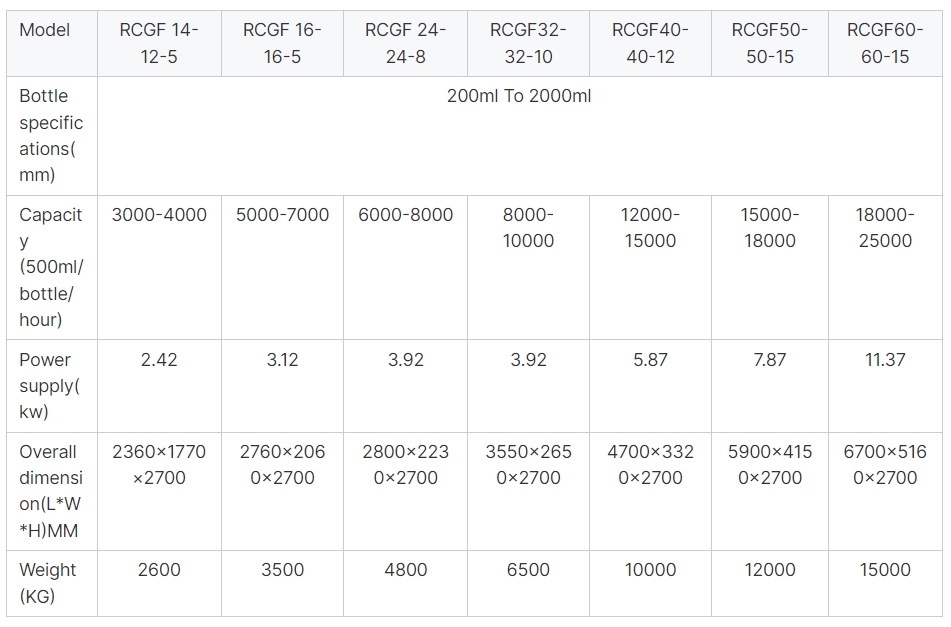